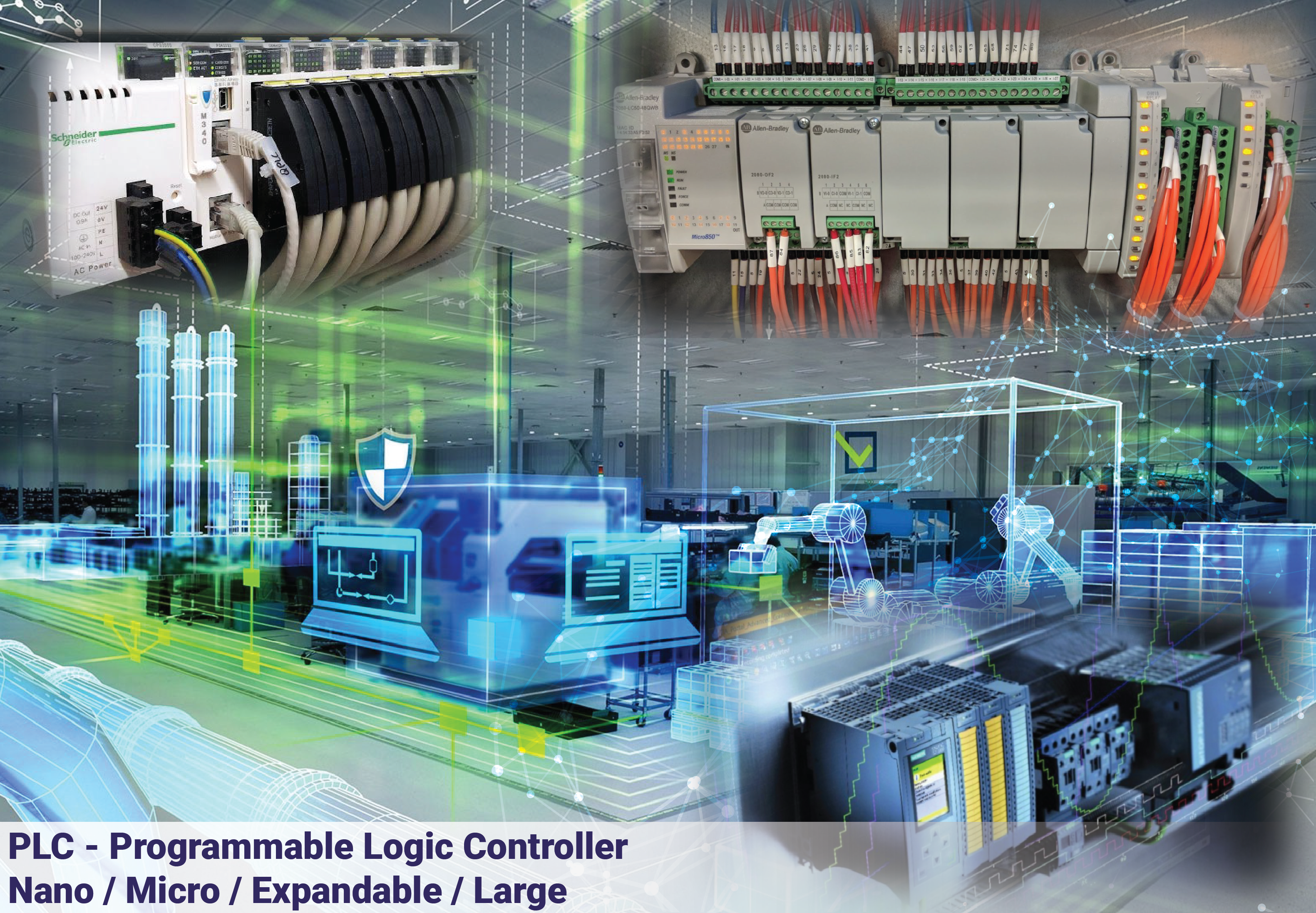
PLC Control Systems
A Programmable Logic Controller (PLC) control system is an industrial digital computer designed to control manufacturing processes, machinery, and other automation applications. Here’s a detailed explanation:
Several companies are well-known for manufacturing Programmable Logic Controllers (PLCs) and offering related automation solutions. Here are some of the most popular PLC companies:
Siemens
– Key Products: SIMATIC S7 Series (S7-1200, S7-1500, S7-300, S7-400)
– Strengths: High reliability, extensive range of products, strong integration with other Siemens automation products, powerful software tools like TIA Portal.
Rockwell Automation (Allen-Bradley)
– Key Products: Control Logix, Compact Logix, Micro Logix, SLC 500
– Strengths: Comprehensive automation solutions, strong presence in North America, robust software support with Studio 5000.
Schneider Electric
– Key Products: Modicon Series (M221, M241, M251, M340, M580)
– Strengths: Wide ranges of PLCs for different applications, strong focus on energy management and efficiency, EcoStruxure platform for IoT integration.
Mitsubishi Electric
– Key Products: MELSEC Series (FX, L, Q, iQ-R)
– Strengths: High-performance PLCs, extensive networking capabilities, integrated solutions for factory automation.
Omron
– Key Products: SYSMAC Series (CP, CJ, CS, NX, NJ)
– Strengths: User-friendly programming environment, strong emphasis on machine automation, advanced motion control capabilities.
ABB
– Key Products: AC500 Series
– Strengths: Scalable and flexible solutions, robust performance in harsh environments, strong support for industrial communication protocols.
Panasonic
– Key Products: FP Series (FP0R, FP-X, FP7)
– Strengths: Compact and cost-effective PLCs, high-speed processing, and integrated communication options.
Bosch Rexroth
– Key Products: IndraLogic Series
– Strengths: Strong integration with hydraulic, pneumatic, and electric drive technologies, robust automation solutions for manufacturing.
Honeywell
– Key Products: Control Edge Series
– Strengths: Focus on process industries, integrated solutions for control and safety, robust cybersecurity features.
Delta Electronics
– Key Products: DVP Series
– Strengths: Cost-effective solutions, strong presence in Asia, integrated with Delta’s drive and motion products.
Keyence
– Key Products: KV Series
– Strengths: High-speed processing, compact design, extensive I/O options, strong support for vision and measurement applications.
Yokogawa
– Key Products: FA-M3 Series
– Strengths: High-speed control, modular design, strong presence in process industries.
Beck Hoff Automation
– Key Products: CX Series, Embedded PC Controllers
– Strengths: PC-based control systems, high performance and flexibility, integration with EtherCAT for high-speed communication.
Key Considerations When Choosing a PLC
Application Requirements:
– Determine the specific needs of your application, such as processing speed, I/O count, and communication protocols.
Integration:
– Ensure compatibility with existing systems and other automation components.
Scalability:
– Choose a PLC that can grow with your system requirements.
Environment:
– Consider the operating environment and ensure the PLC can withstand conditions like temperature, humidity, and vibration.
Support and Service:
– Look for manufacturers with strong technical support and service networks.
Software Tools:
– Evaluate the programming software for ease of use, functionality, and support for different programming languages.
Cost:
– Balance the initial investment with long-term benefits such as reliability, maintenance, and ease of use.
These companies represent the leading edge of PLC technology, providing reliable and innovative solutions for various industrial and automation applications.
PLC Training Ahmedabad
PLC Courses Ahmedabad
PLC Certification Ahmedabad
Best PLC Training Institute Ahmedabad
PLC Programming Training Ahmedabad
Advanced PLC Training Ahmedabad
PLC SCADA Training Ahmedabad
Siemens PLC Training Ahmedabad
Allen Bradley PLC Training Ahmedabad
Industrial Automation Training Ahmedabad
PLC Training Center Ahmedabad
PLC Workshop Ahmedabad
Affordable PLC Training Ahmedabad
Professional PLC Training Ahmedabad
PLC Training for Beginners Ahmedabad
PLC Training with Job Placement Ahmedabad
Hands-on PLC Training Ahmedabad
PLC Training Courses Near Me Ahmedabad
Certified PLC Training Ahmedabad
PLC Training Classes Ahmedabad
Training Program | PLC Control System |
Mode of Learning | On Line / Off Line / Work Shop / Company Floor / Plant Floor |
Offline Locations | Ahmedabad / Surat / Baroda / Rajkot |
Online Locations | PAN India, All Cities in India,America/ Europe/ Middle East – International Timings are available |
Eligibility / Engineering Branches | Students from 10th 12th ITI, B.E B. Tech Degree /Diploma / Masters /Graduates Electrical / Electronics / Instrumentation / Mechatronics / Power Electronics , B.Sc., M.sc from Electronics , Physics , Working Professionals |
Duration | 1 Month / 30 Days / Customized |
Contents | Standard & Advance |
Supplements | Demo Software, Examples, Theory, Practical Reading Materials Included |
Placements | Jr. Engineer / Project / Site / Field/ Programmer / |
Companies | OEM / System Integrators / Manufacturing Companies / MNC |
Salaries | 25,000 – 35,000 for Fresher / Experienced |
Components of a PLC System
- Central Processing Unit (CPU):
– The brain of the PLC.
– Executes control instructions based on the programmed logic.
– Manages communications with other components.
- Power Supply:
– Provides the necessary power to the PLC and its modules.
– Typically converts AC voltage to the required DC voltage.
- Input /Output (I/O) Modules:
– Interfaces for sensors and actuators.
– Input Modules: Receive signals from sensors (e.g., temperature sensors, switches).
– Output Modules: Send signals to actuators (e.g., motors, valves).
- Programming Device:
– Used to write and download programs to the PLC.
– Can be a computer with PLC programming software.
How a PLC Works
- Input Scan:
– The PLC reads the status of all input devices.
– Converts physical signals (e.g., ON/OFF states) into data the CPU can process.
- Program Execution:
– The CPU executes the control program stored in its memory.
– The program is typically written in a specialized programming language, like Ladder Logic, Function Block Diagram (FBD), or Structured Text (ST).
- Output Scan:
– The CPU sends signals to the output devices based on the program logic.
– Converts processed data back into physical signals to control actuators.
- Housekeeping:
– Includes internal diagnostics, communication tasks, and other maintenance activities.
PLC Programming Languages
- Ladder Logic:
– Resembles electrical relay logic diagrams.
– Easy for those with an electrical background to understand.
- Function Block Diagram (FBD):
– Uses blocks to represent functions and connections to represent data flow.
– Ideal for complex algorithms and process control.
- Structured Text (ST):
– High-level programming language similar to Pascal.
– Suitable for complex mathematical operations and algorithms.
- Sequential Function Chart (SFC):
– Graphical representation of sequential control processes.
– Useful for batch processes and step-by-step operations.
Applications of PLC Control Systems
– Manufacturing Automation:
– Assembly lines, robotic arms, CNC machines.
– Process Control:
– Chemical plants, water treatment facilities, food and beverage processing.
– Building Automation:
– HVAC systems, lighting control, security systems.
– Transport Systems:
– Elevator control, conveyor systems, automated warehousing.
Advantages of PLC Control Systems
– Reliability and Durability:
– Designed to withstand harsh industrial environments.
– Flexibility:
– Easily reprogrammed to adapt to different tasks.
– Scalability:
– Can be expanded with additional I/O modules.
– Reduced Wiring:
– Simplifies control panel design and wiring.
Example Use Case
Consider an automated packaging line where a PLC is used to control the process:
- Inputs:
– Sensors detect the presence of products on the conveyor belt.
– Temperature sensors monitor the heat-sealing process.
- Processing:
– The PLC program counts products, controls the conveyor speed, and manages the heat-sealing cycle.
- Outputs:
– Actuates motors to move the conveyor.
– Activates heating elements for sealing.
– Controls robotic arms for packaging.
The PLC constantly scans inputs, executes the program, and updates outputs to ensure smooth operation of the packaging line.
In summary, a PLC control system is a robust, flexible, and reliable solution for automating industrial processes, enhancing efficiency, and ensuring precise control over machinery and processes.